The Importance of Loft Insulation: Maximizing Comfort and Energy Efficiency
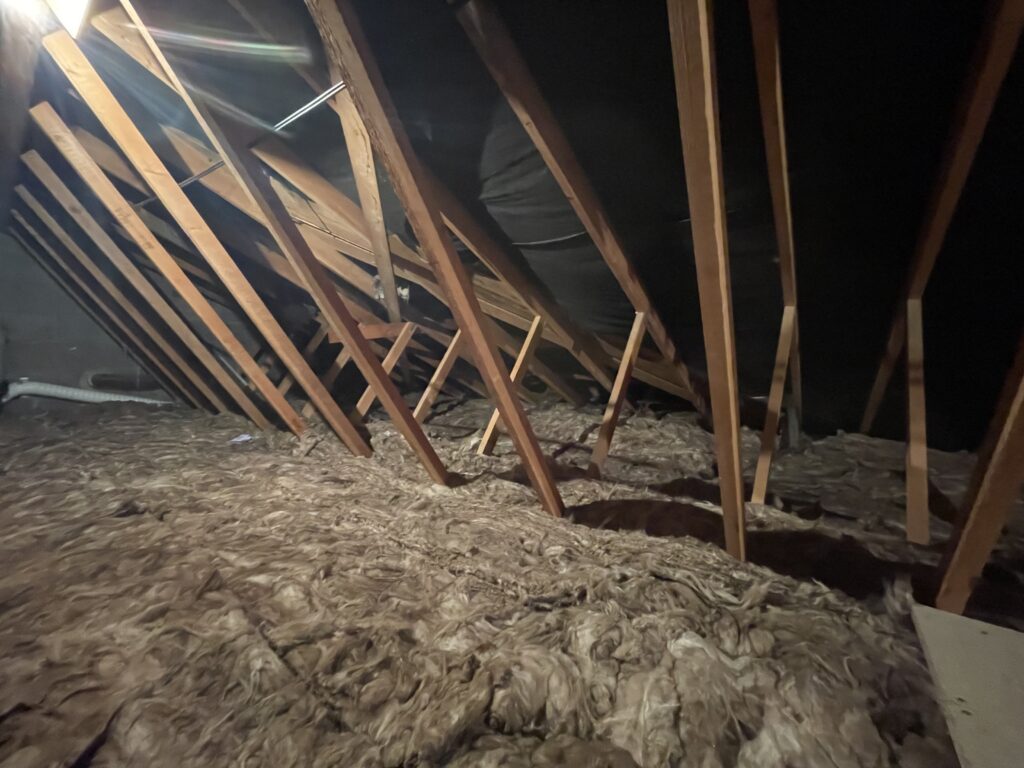
Loft insulation is vital for a comfortable home and energy efficiency. As energy costs rise, proper loft insulation becomes increasingly essential for homeowners. It effectively helps reduce both bills and your carbon footprint.
What Is Loft Insulation?
Loft insulation involves adding material between your ceiling and roof, which minimizes heat loss in winter and keeps your home cooler in summer. Common materials include fiberglass, mineral wool, and spray foam, each offering unique benefits for thermal performance and installation ease.
Benefits of Loft Insulation
- Energy Efficiency: Notably, good insulation can cut energy use by up to 25%. It helps maintain a stable indoor temperature, resulting in lower energy bills and less demand on heating and cooling systems.
- Comfort: Furthermore, insulating your loft creates a consistent temperature throughout your home. This effectively eliminates cold spots and drafts, leading to a more comfortable living environment year-round.
- Environmental Impact: Additionally, loft insulation reduces energy use, which lowers your carbon footprint. This aspect is crucial in addressing climate change, as energy production significantly contributes to greenhouse gas emissions.
- Increased Property Value: Moreover, homes with effective insulation attract more buyers. Energy-efficient properties can command higher prices and sell faster in today’s market.
Green Horizon Energy Solutions Ltd: Your Partner in Loft Insulation
For homeowners looking to improve energy efficiency, Green Horizon Energy Solutions Ltd offers tailored expert services. They focus on sustainability and innovative energy solutions, providing professional assessments and installations of loft insulation.
Our experienced professionals ensure your home is properly insulated. By using high-quality materials and the latest techniques, they maximize your investment, helping you save on energy bills while reducing your environmental impact.
Installation Tips
If you’re considering loft insulation, keep these essential tips in mind:
- Choose the Right Material: First, evaluate different insulation materials to find the best fit for your home’s needs.
- Check for Gaps: Next, look for gaps in your insulation to prevent heat leaks. Sealing air leaks significantly boosts insulation effectiveness.
- Consider Professional Installation: While some may opt to install insulation themselves, hiring professionals like Green Horizon Energy Solutions Ltd ensures the job is done correctly and efficiently.
Conclusion
In conclusion, loft insulation is a worthwhile investment for comfort, energy savings, and environmental responsibility. Whether you’re building a new home or upgrading, consider the long-term benefits of proper insulation. With Green Horizon Energy Solutions Ltd, you can create a cosy, efficient home that lasts. Their commitment to sustainability ensures that your project not only improves your home but also benefits the environment.
- Published in Uncategorized
Unlocking Space and Efficiency: Green Horizon Energy Solutions Loft Boarding Services
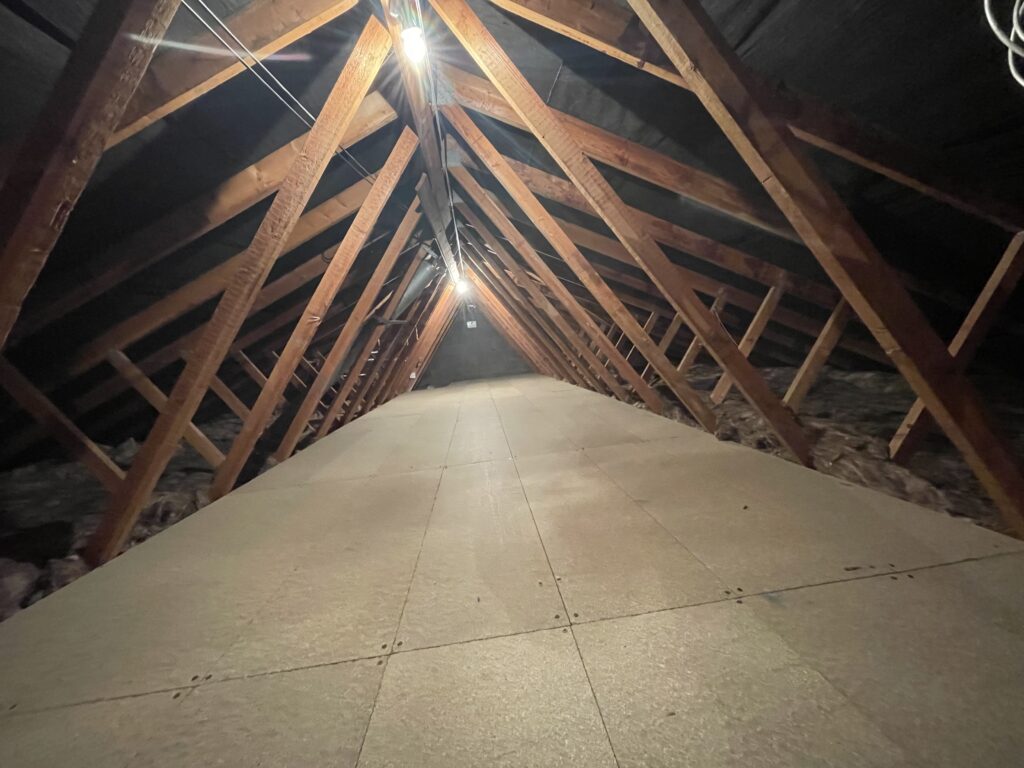
Green Horizon Energy Solutions offers innovative loft boarding services. We focus on maximizing living space and improving energy efficiency in homes. A key feature of our service is the raised loft leg system. This method keeps your insulation intact while providing a strong storage platform.
The Importance of Loft Boarding
Loft boarding is a great way to use the often-overlooked space above us. It provides extra storage for seasonal items, holiday decorations, and more. Boarding your loft can make a big difference. However, many homeowners worry about damaging insulation or reducing energy efficiency.
Our Raised Loft Leg System
At Green Horizon Energy Solutions, we prioritize both functionality and energy efficiency. Our raised loft leg system is a game-changer in loft boarding. Here’s how it works:
Preservation of Insulation: Traditional loft boarding methods often compress insulation, which reduces its effectiveness and can lead to potential heat loss. However, our raised loft leg system elevates the boarding above the insulation. As a result, it prevents any compression and allows the insulation to perform optimally.
Sturdy and Safe Platform: Moreover, the loft legs provide a secure foundation for the boarding. This ensures that it can hold weight without sagging or shifting. Consequently, you can store your items with peace of mind, knowing that the structure is reliable.
Easy Access: In addition to focusing on the structural integrity of your loft, our service also considers accessibility. With properly boarded lofts, accessing your stored items becomes a breeze. For added convenience, you can easily install a loft ladder or hatch for more convenient entry.
Energy Efficiency: Furthermore, by maintaining insulation integrity, our loft boarding solutions help reduce heat loss in your home. This, in turn, can lead to lower energy bills and a more comfortable living environment. Therefore, it makes for a wise investment for any homeowner.
Why Choose Green Horizon Energy Solutions?
Expertise and Experience – Our team of professionals has extensive experience in loft boarding and energy efficiency solutions. We understand the unique needs of each home and tailor our services accordingly.
Quality Materials – We use only high-quality materials that ensure durability and longevity, providing you with a loft space that will serve you well for years to come.
Customer Satisfaction – Our commitment to customer satisfaction means we work closely with you throughout the process, ensuring all your questions are answered and your needs are met.
Conclusion
Green Horizon Energy Solutions is dedicated to helping you unlock the full potential of your home while prioritizing energy efficiency. Our loft boarding services, utilizing a raised loft leg system, are designed to provide you with a functional, safe, and energy-efficient storage solution. Don’t let your loft space go to waste—transform it today with our expert services and enjoy the benefits for years to come!
For more information or to schedule a consultation, contact us today!
- Published in Uncategorized
Water Leaks in Air Conditioning – Causes and Solutions
Not all air conditioning issues require a call out – here are some of the common causes and our solutions to fixing them
How does it work?
An air conditioning system works by passing cold gas through a coil, which, in turn, cools the warm air as it passes over it. Consequently, as warm air passes over the coil and cools, it causes water in the air to condense onto the coil.
Moreover, the air conditioner has a drip tray located below the coil on the inside unit. Condensation that forms on the coil drips into the tray and should flow to either a drain or the outside of the property.
Additionally, some drip trays connect to a gravity-fed drain and run directly outside. However, other trays connect to a condensate pump where they can’t drain by gravity and may need to pump up and over.
Blockages
Sometimes debris blocks these drains. By locating the drain tube on the outside of the building, you can check the end for a blockage. You can also gently blow down the tube. If the air flows freely, it should be clear. Be prepared for some water to come back at you if you dislodge a blockage—you don’t want a face full of water!
Knowing Your Tubes
There are generally two types of drain tube. The pictures below should help you identify the types. The larger corrugated tube in most cases is a gravity-fed tube. The small thin tube generally attaches to a condensate pump. The good news is that clearing a gravity-fed tube should be easier. Tubes connected to condensate pumps most likely need a professional to check the pump is working and to ensure the blockage is not within the float side of the pump.
Condensate Pump Tube & Corrugated Gravity Fed Drain Tube
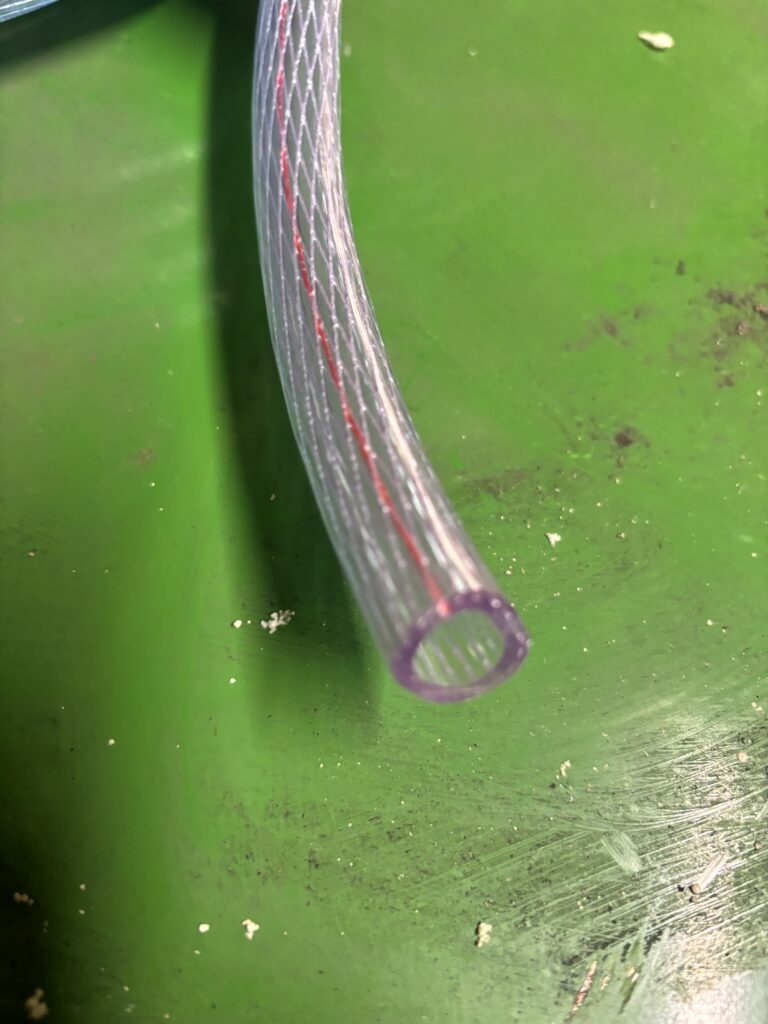
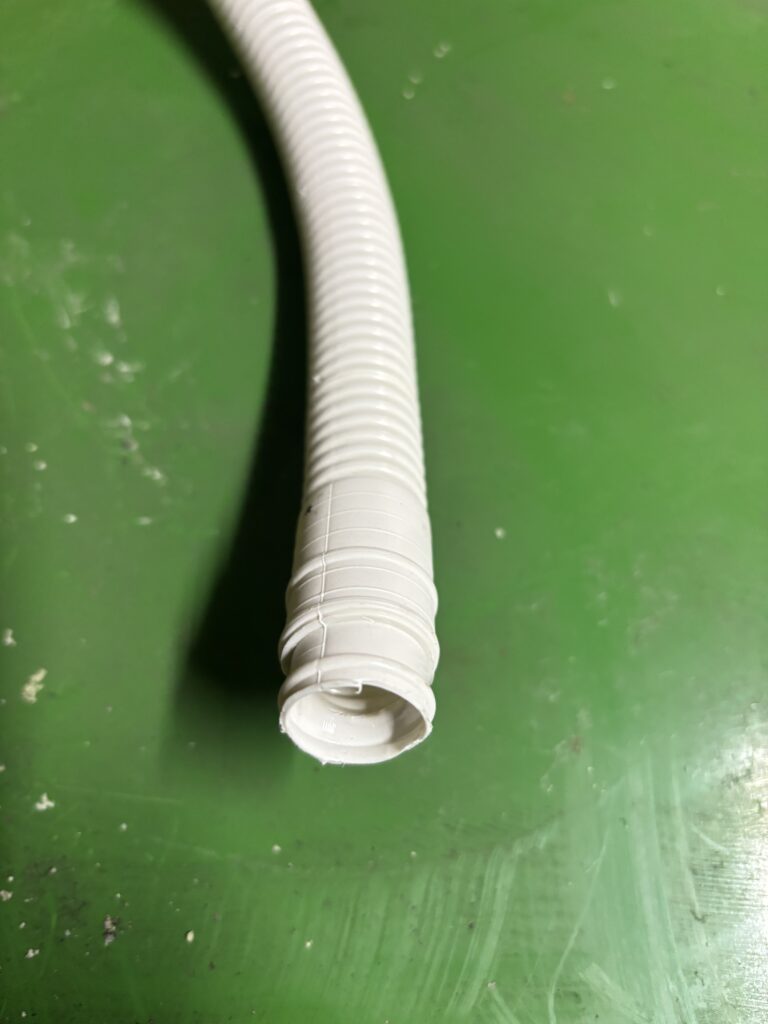
Gas Issues
Another cause of dripping water can be due to low gas. Low gas and lower pressure can cause water on the coil to freeze and build up. Sometimes when the unit is switched off the ice will melt. Due to the excess volume of water it can’t be drained away quick enough, causing the drip tray to overflow.
Most units have a secondary rear drip tray, this is much smaller than the main one. These trays feed into the front tray for any water to be drained away with the rest. As with the main tray this can get clogged.
Keeping on top of Maintenance
It’s important for units to undergo regular maintenance to remove any buildup of dust and dirt. Consequently, this ensures the machine is working fully. Therefore, we recommend using a qualified engineer for annual servicing to avoid such problems.
Furthermore, there are special cleaning solutions available to help keep drains clear. These solutions are simple to use and can be sprayed onto the coil at the front, underneath the filter, and do not require rinsing. Simply spray on and leave to work while setting the unit to self-cleaning mode. Additionally, it’s a good idea to do this at regular intervals to avoid a buildup of dirt.
If in doubt, always call a professional.
Finally, we are available for servicing and fault finding of all split system domestic and light commercial air conditioner/heat pumps.
Call our experienced team on 0161 427 0772, or email us at info@greenhorizonenergy.co.uk
- Published in Uncategorized
Stockport Market – Insulating a Piece of History
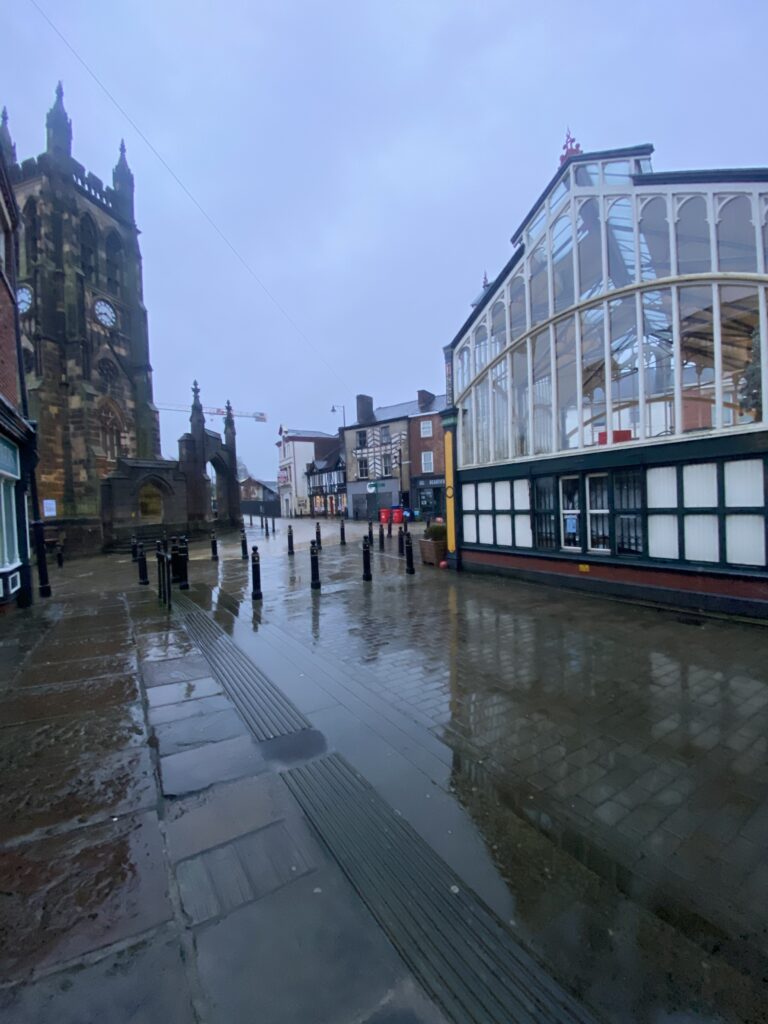
Tackling History
One of our latest projects was to insulate the loft of a 200 year old listed building adjacent to the iconic Stockport market. This commercial property offers retail storage space and a shop front spread over three floors. There was a new tenant taking over the lease and the Landlord was concerned about a lack of insulation.
Survey Findings
The team at Green Horizon Energy Solutions Ltd undertook a site survey. This confirmed the Landlords concerns, a lack in insulation. Considering the age of the property at 200 years old, the roof was in excellent condition. A breathable roof felt indicated that there had been a new roof not too long ago. Original slates were present from the outside, indicating they had been reclaimed and re-installed on top of a modern roof felt. At ceiling level, the joists looked to be a mix of new and old timber, clearly having some work done to strengthen the integrity of the old ceiling.
The Work
First Green Horizon Energy Solutions installation team laid a base layer of 100mm Knauf roll out insulation between the joists. Then followed an additional layer of 200mm Knauf roll was laid across the top. Care was taken to make sure sufficient air flow at eves level was left free for ventilation above the insulation and to prevent any issues with condensation.
Outcomes
The total 300mm of insulation provides a U value of circa 0.15 offering great thermal resistance for the commercial property. Energy costs will be cut for the tenant and it will also provide a comfortable environment to work in. Don’t just take our word for it though – our customer left us a 5* review on Google.
“Good service from initial contact to insulation being installed.
Excellent communication!
Highly recommended!”
This can be found: https://g.co/kgs/iyp4aiV
- Published in Uncategorized
The effects of Radiated heat and underfloor insulation
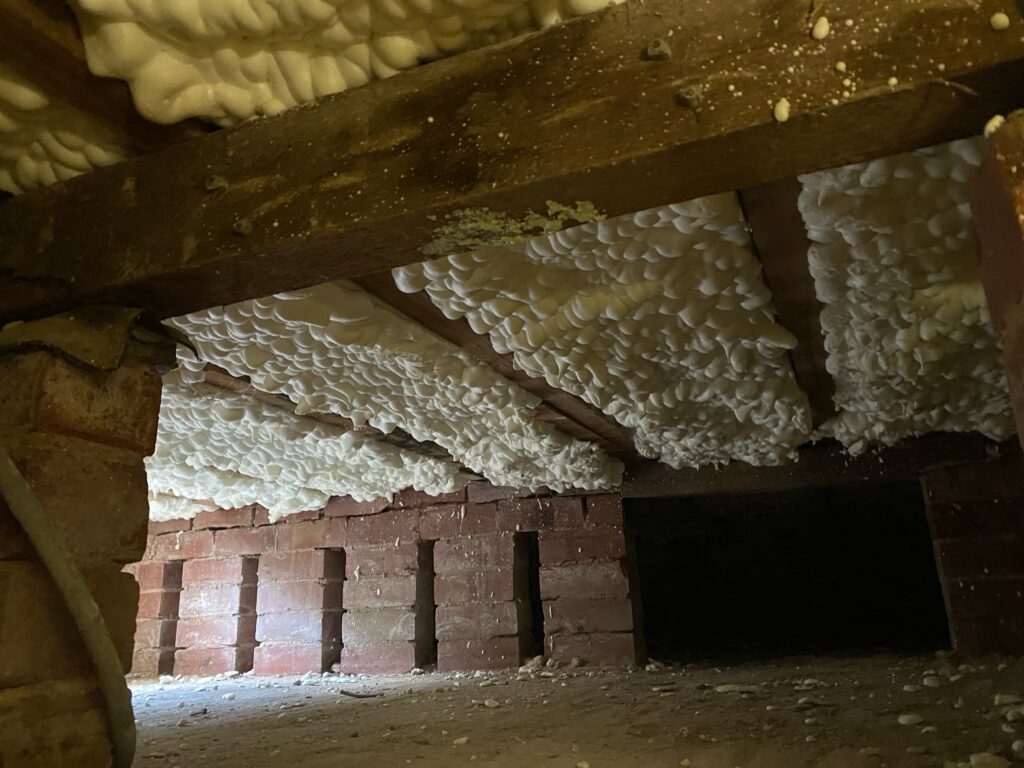
Heat is given off by all objects in your home if the surfaces around you are colder than you, heat will transfer from you to them and if they are warmer than you, they will give heat to you.
This is one of the reasons why people find underfloor insulation so effective. The reports from our clients show that they never expected it to make such a huge difference to the comfort they feel in their home.
Uninsulated Floors
If you have an uninsulated floor void exposed to cold outside air, this will lower the temperature of the floor. With such a vast surface area, a cold floor draws radiated heat from the body. This effectively sucking the heat from you. Insulating the floor void and raising the temperature of the floor boards you can reduce this radiant heat transfer. Heat exchange happens faster at higher temperature differentials, raising the temperature of the floor by just a few degrees can slow the transfer of heat between yourself and the cold floor boards.
Don’t blame the air temp…
Have you ever noticed when winter comes you reach for the thermostat, cranking it all the way up to 25c. Yet on a hot summers day, there is nothing better than sitting in an air conditioned room at a chilly 16c. This has a lot to do with radiant heat and shows that air temperature is not the only factor at play when trying to reach a comfortable temperature within your home.
All this comes into play on top of the other benefits you get for adding underfloor insulation, like eliminating draughts that come up through gaps in floorboards or around openings for pipes and wires.
Cavity wall insulation is another great example of the importance of radiant heat transfer.
To find out more or for a free no obligations quote – give us a call on 0161 427 0772
- Published in Uncategorized
Think its too hot for insulation?
Whilst the UK temperature is hitting a current yearly high, it’s no surprise that improving your homes insulation has hit the bottom of your to do list. But here’s the thing, thermal efficiency isn’t just for Christmas!
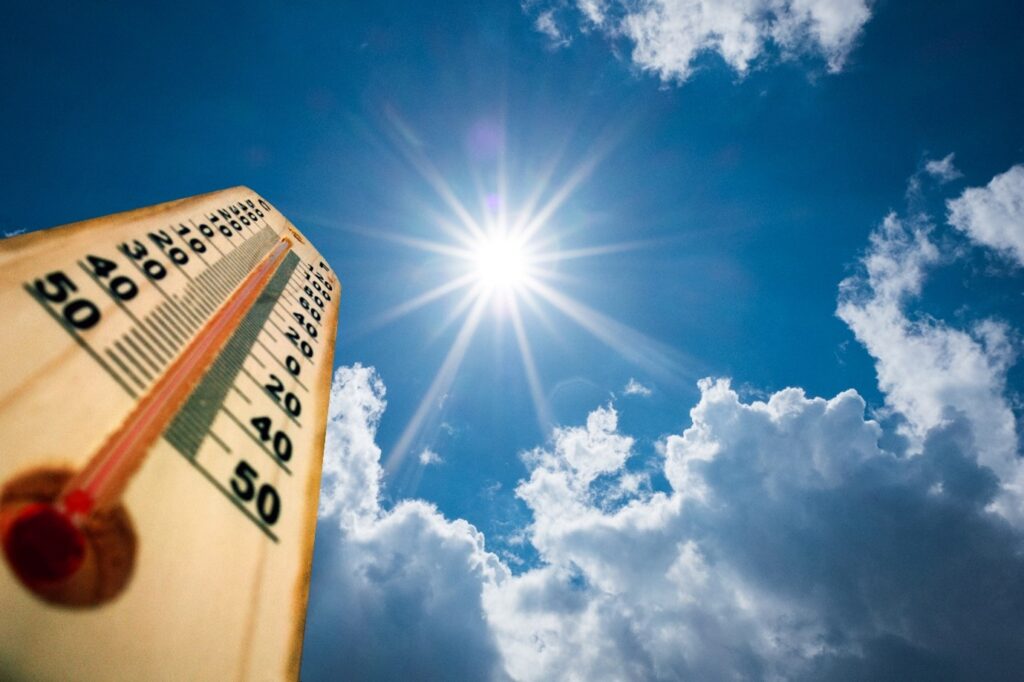
Insulating a home, isn’t solely about gaining a warmer home. Its about regulating your temperature.
Think of your house like a thermos flask. Whatever is inside the thermos you want to keep warm for as long as possible, but we also use thermos for keeping things cool. The product isn’t designed just for warmth – its aim is to regulate the temperature of the product inside and slow down the heat transfer. Keeping the warm air out for a cold drink, or the warm air in for a hot soup.
This is the exact same for spray insulation and your home. Spray foam doesn’t create heat, or cold. It simply ‘traps’ it. Keeping your home at a more stable temperature for longer.
At Green Horizon Energy Solutions – our open cell spray foam is a perfect solution for slowing the transfer of heat. We use a product called H2foam lite E from Huntsman. This was originally developed for use in timber framed houses in Canada which have to accommodate hot summers and freezing conditions in winter. For more information about how we can help you insulate your home please get in touch.
Keeping cool
Here are a few more tips to help keep the heat at bay.
- Close your curtains, especially where windows are in direct sunlight. Blocking out some of those hot rays will see the room temperature avoid those dizzying heights.
- Close doors on those cool rooms. You really want to keep those rooms as little cool havens in your home, so where you have a cooler area of the home, make sure you keep it that way. This also applies in reverse. If you have a room that is an oven and you don’t need to be in there – then keep that heat away from the rest of the home by shutting it in.
- Create your own air con – if you have a fan you can easily do this. Place a shallow bowl of ice in front of the fan and feel the cooled air blowing your way.
- Published in Uncategorized
Underfloor insulation – Spray foam vs traditional insulation materials
Underfloor insulation is an effective way to reduce energy costs and create a more comfortable environment within your home.
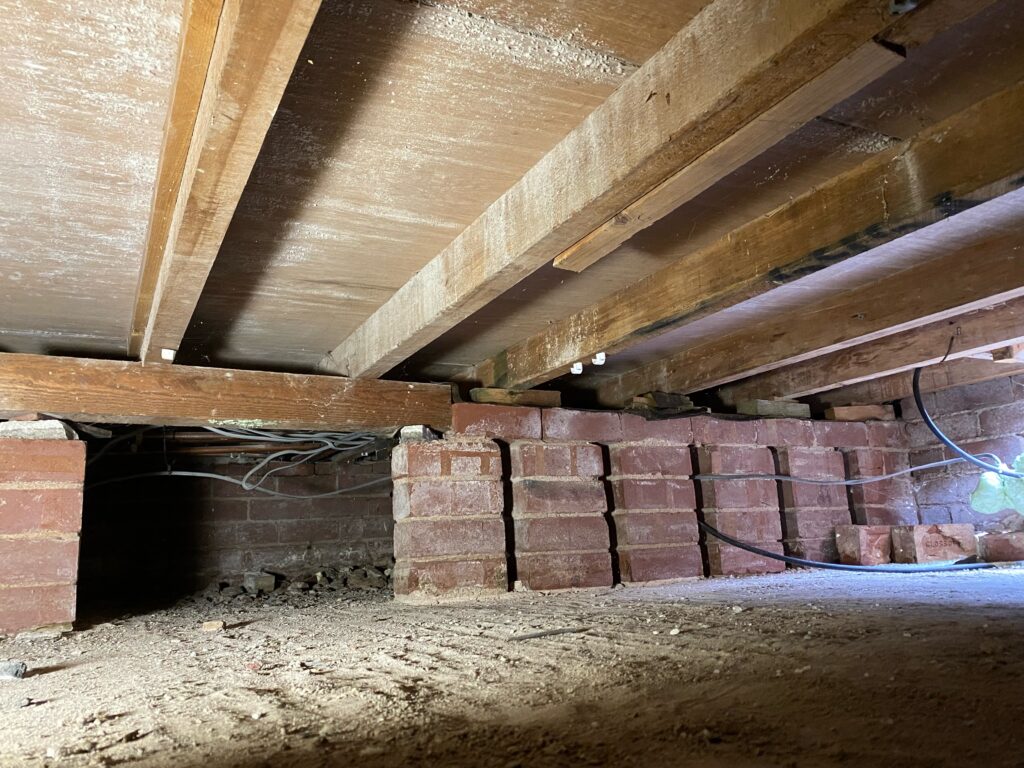
Survey says – don’t forget your toes
Underfloor insulation is one of the biggest areas for improvement in your home, yet it is vastly overlooked by most people.
If you were to do a survey about improving insulation within a home, you could guarantee most people would say loft first followed by walls, without giving a thought to the floor. Obviously heat rises, but it doesn’t just rise – it can move in any direction depending on the pressure difference.
Suspended floors – what you need to know
Most older homes, especially those built from the 1900’s through to the 1970’s were built with a suspended timber floor. At the time of construction, these were not considered necessary to insulate. The space below the floor was built as a ventilated space. Airbricks placed in the external walls allow for ventilation and prevent moisture problems within the timbers. However, these airbricks can cause unwanted draughts, making floors cold to touch. This is caused by the floor being exposed to outside temperatures.
An expansion gap runs along the perimeter of the house, allowing the building to expand and contract with seasonal changes to temperatures. This expansion gap can cause draughts to trickle into the main body of the house. As heat rises within the property, this also causes what is know as the stack effect. This is where cold air gets drawn in to replace the warm air as it rises.
Beating the chills
One way to combat cold floors is to insulate them. Using traditional forms of insulation such as fibre rolls, can provide some benefit. However, in the main this is not overly effective. Fibre insulation is not an air barrier material so the cold air circulating below the floor cuts through the material. Its a bit like wearing a woolly jumper whilst stood on top of a windy hill. Although you’ll feel some thermal benefit, the wind will get through the holes that naturally appear. You would be better off with a windproof jacket that is airtight.
The expansion gap is also an issue when using fibre material as you can very rarely get the insulation into the gap with any effectiveness. Fibre materials will require some sort of netting in place to stop the material from falling out of place. This can make it a difficult job to complete. Even when it is possible to net the material in place, it will sag over time and will loose more of its thermal resistance.
PIR Boards – pros & cons
A newer way to insulate a suspended floor, would be to use rigid PIR board insulation. Although ridged board insulation does offer great thermal resistance and the boards themselves don’t allow air to pass through, they have their own set of issues.
To install rigid board effectively they need to be cut to size to fit tightly between the floor joists. The boards usually require to be foamed in round the edges with expanding foam from a can. Leaving as little as a 5% gap round the edge can equate to a 50% loss in thermal efficiency, akin to buying a fridge and leaving the door open, it’s just not effective.
Again, as above the expansion gap is an issue, if not worse when using rigid boards. It’s impossible to get the insulation into the gap effectively and the lack of movement in the board would restrict the properties’ ability to expand and contract.
Leading the way
Open cell spray foam insulation is one of the newest ways to insulate a suspended timber floor and a lot of the issues mentioned with the other two methods are mitigated. Open cell foam is a breathable material. It will allow timbers to continue to breathe as they should. As long as the air bricks are left clear this will prevent issues with moisture.
Open cell foam will stick directly to the underside of the floorboards, meaning you don’t need any type of fixing to hold it in place. It will not sag or degrade over time and comes with a 25 year warranty.
Open cell foam expands 100x on application. This makes it easy to fill the expansion gap and eliminate draughts. Open cell foam does not set hard and remains soft and flexible so filling the expansion gap is viable as it still allows expansion and contraction moving with the seasonal changes.
Open cell – gets our vote
With all this said, hopefully it gives you a good insight into why we believe open cell foam is the most effective solution for insulating a suspended timber floor.
We have been insulating suspended timber floors since 2016 with great effect and amazing feedback from our clients. Some clients report energy savings of 30% and all of our clients saying what a noticeable difference it has made to the comfort of their home.
- Published in Uncategorized
Spray Foam Insulation for Shipping Containers
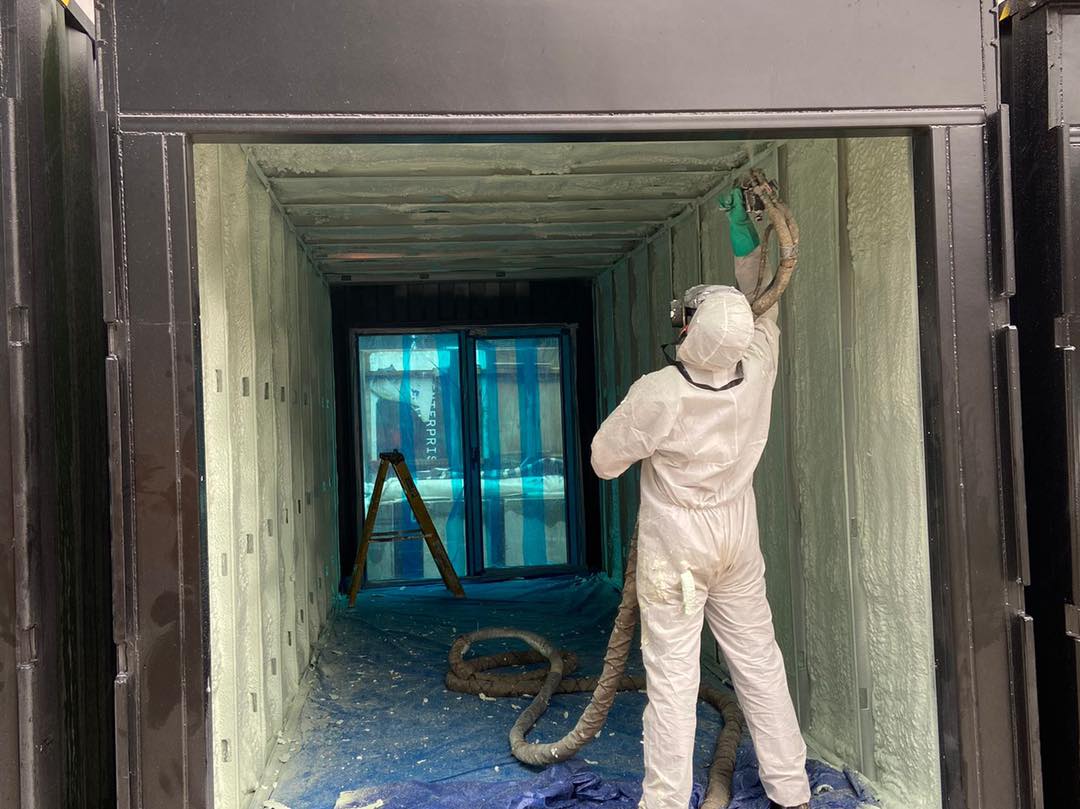
Traditional Insulation Pit Falls
Choosing the correct insulation for a shipping container is critical to preventing issues with condensation. The way shipping containers are built, means the walls are not flat. This makes it impossible to get any traditional form of insulation to follow the contour of the outer skin without gapping. This causes issues as it leaves a cold surface behind the insulation where condensation can form. With the lack of ventilation on the cold side, moisture can become trapped. This can be bad news for the container & contents alike.
Why consider Spray Foam
Spray foam insulation bonds directly to the surface, following the contour of the outer skin. This removes cold surfaces for condensation to form on as there is no longer a gap. There are two types of spray foam, open cell and closed cell. Closed cell spray foam is the most suitable for a shipping container due to the vapour resistance of the product. Another advantage for closed cell is a thinner application can be used. With a thinner spray, your shipping container loses less space. This ensures the maximum room is left to utilise for your project.
Boarding
If you plan to board over the insulation, you will need to choose a suitable frame to fix the boards to. These frames can be timber or metal. Ideally you want to stand the frame off from the external wall. This allows the insulation to fill the space behind the frame and helps eliminate cold bridging.
Vapour Barrier
Before boarding, for extra protection we advise fitting a suitable vapour barrier over the insulation. Although closed cell insulation has a high resistance to moisture, it is still only a vapour retarder. There is a difference between a vapour retarder and a vapour barrier. In most cases closed cell foam on its own is enough to stop moisture and condensation build up. For extra protection and where the foam is to be boarded over, we would advise an additional vapour barrier to be fitted.
Flues and Other Heat Generating Appliances
When fitting a flue for a boiler or heater, make sure this is suitably protected from direct contact with the insulation. Also consider adequate ventilation for combustion reasons. Seek advice from the installers or manufacturers of these appliances about their requirements prior to installation to avoid any issues later down the line.
Help Is At Hand
Green Horizon Energy Solutions will guide you through the best practices when it comes to insulating your shipping container. Whatever the purpose – storage, office or workshop, we ensure the insulation is fit for your needs. We work with you to make sure building regulation requirements are met to create the perfect habitable space to meet your requirements.
- Published in Uncategorized
The Benefits of Spray Foam Insultation
Spray foam Insulation has become a popular choice for homeowners in recent years, and for good reason. It offers many benefits that traditional insulation methods cannot match. In this article, we will discuss the benefits of spray foam insulation in homes.
- Energy Efficiency
One of the primary benefits of spray foam insulation is its ability to create an air-tight seal in your home. This seal prevents air leaks and draughts that can significantly reduce your home’s energy efficiency. With spray foam insulation, you can save up to 50% on your energy bills by reducing the amount of heating and cooling needed to keep your home comfortable. The savings on your energy bills can offset the cost of the insulation in a few years.
- Improved Air Quality
Spray foam insulation creates an air-tight seal, which means it can help prevent outdoor pollutants and allergens from entering your home. This feature can help improve indoor air quality, especially for those who suffer from allergies or respiratory problems.
- Soundproofing
Spray foam insulation has excellent soundproofing properties that can reduce noise pollution. The insulation can help keep out unwanted sounds from outside, such as traffic or barking dogs, and it can also help to reduce noise transfer between rooms inside your home.
- Long-Lasting
Spray foam insulation has a lifespan of the building, which is significantly longer than other types of insulation. This lifespan means you won’t have to worry about replacing the insulation for several decades, saving you time and money in the long run.
- Versatile
Spray foam insulation can be used in a variety of applications. It can be used in walls, ceilings, and floors, making it a versatile option for homeowners. Additionally, it can be applied to irregularly shaped spaces, making it a perfect solution for hard-to-reach areas that are difficult to insulate using traditional methods.
In conclusion, spray foam insulation offers many benefits that traditional insulation methods cannot match. It can help to save on energy bills, improve indoor air quality, reduce noise pollution, last for decades, be used in a variety of applications, and is environmentally friendly. If you are considering upgrading your home’s insulation, it’s worth considering spray foam insulation for the benefits it offers.
- Published in Uncategorized
Combating Energy Price Rises
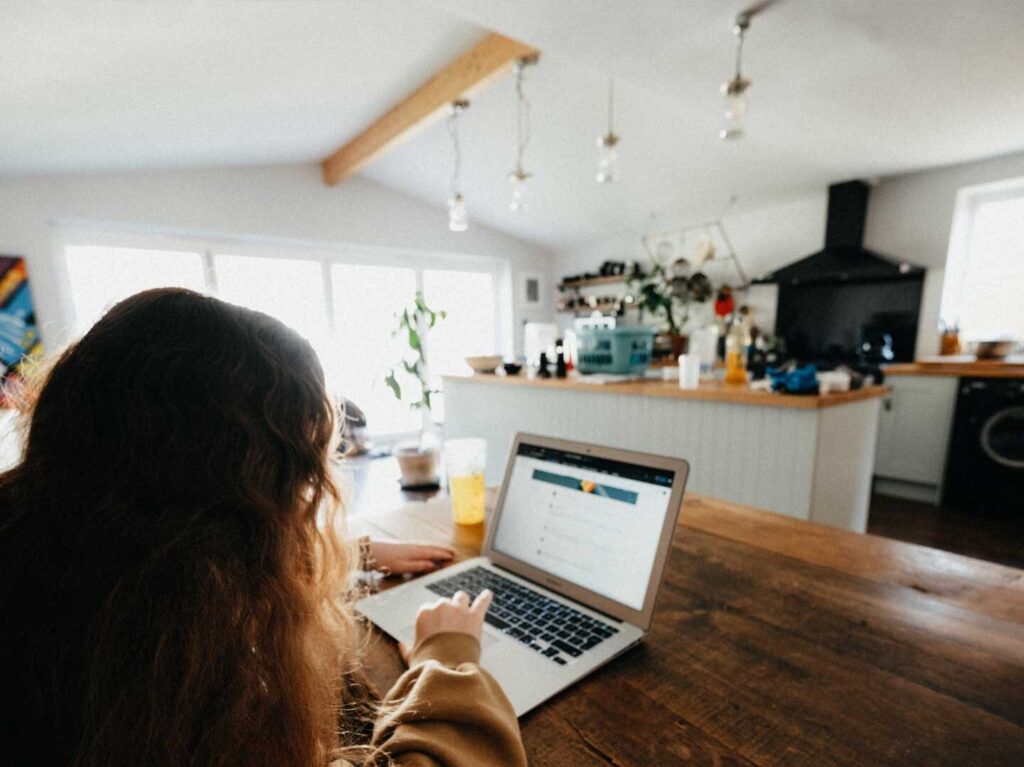
UK Prices Set to Rise…
2022 saw sharp rises in energy prices across the whole of the United Kingdom. The energy bill support scheme (EBSS) took some of the burden with £400 automatically funded from the government to households in order to help with energy costs. However, from the 1st of April 2023 this will come to an end and prices are set to rise again. Households could see a further 20% added to their monthly bills.
That said, the Energy Price Guarantee has been extended for an additional 3 months until June. Hopefully bridging the gap through to the summer, when most of us (hopefully) won’t be using the heating. This is the UK though, so who knows what our weather will bring!
The Energy Price Guarantee limits the amount suppliers can charge per unit of energy used. The EPG will bring the average typical household in Great Britain to £2500 per year.
From the 1st of April to the 30th of June, the Ofgem energy price cap level is £3,280 annually. This is what you would pay if the EPG was not in place.
Watching the Pennies…
The UK has a vast number of older housing stock. Many of which are poorly insulated and are draughty homes leaking energy like sieves. Older regulations were less strict on the amount of insulation a home required at the point of build. This teamed with energy prices which were so cheap, it was never much of an issue for homeowners who could leave the heating on or throw more coals on the fire.
Over the years things have changed. As global warming takes a hold, we have learned we can’t continue burning fossil fuels without affecting the environment. Newly built homes have much stricter regulations regarding thermal efficiency. When built to a good standard, they are far more energy efficient than they used to be.
It’s not just global warming that’s at the front of people’s minds, but also the cost of energy. Huge price rises are putting families under pressure to find ways to save money on their energy consumption. It’s not just for heating though, also overall usage is coming under the spotlight, whether that be using more energy efficient appliances or changing the way they operate their households in general. There are numerous things you can do to reduce your energy consumption. Whether you wish to do this to play your part in easing global warming or if you are looking to reduce your energy costs.
Bigger Picture Thinking…
Steps to reduce energy consumption can be as simple as turning a TV off, not just leaving it on standby. We understand on an individual basis, this is not likely to make a noticeable difference to your energy bills. As a collective though, if the nation were to do this we could reduce the countries global warming impact. Small steps taken by millions of people, could make a huge difference. It’s often the small steps taken individually that lead to bigger changes collectively.
Every small energy saving step you take in your home will add up over a year. It might not be a huge amount but it could be enough to treat the family to a nice takeaway or towards a family day out. At the end of the day, that extra money is better in your pocket than with the energy companies. If you’re not bothered about the amount you could save each year, just remember, that money is going to the energy firm and a small amount of money from everyone soon adds up and turns into hundreds of thousands of pounds if not more. All this money collectively could be going to your local economy and supporting individuals like yourselves in their local businesses instead.
Small Steps to Change…
Some other things you can do to reduce your energy bills are:
- Turn off lights in rooms you’re not in.
- Turn down boilers and hot water temperature.
- Only boil the amount of water you need & switch it off just before it boils, after all who drinks water at 100c anyway. Tea will still brew nicely at 80c and it’s amazing how much energy you can save by not heating that water the extra 20c.
- ‘Shut that door’ as my mum would say. It sounds daft, but when anyone leaves my house I tell them to get out quick and close the door. Get your coat on, open the door step out and close it straight away. You’ve paid to heat the room, don’t let that blast of cold get in!
- Look at the energy ratings of appliances. I’m not suggesting you go out and buy new appliances for the sake of it, but when it’s time to renew things take note of the energy rating and think how much it could save you in the long run.
- Avoid using the tumble dryer when you can. I’m guilty of this especially in winter. Try to dry a decent amount at once. Drying on radiators can cause moisture issues in a property and covering the radiator with wet clothes is costly as it blocks the radiator from heating the room as it should.
- The same goes for washing machines. Make sure you have a decent load in at once and with the effectiveness of detergent, it’s just as effective to run on a cooler wash.
- Spend less time in the shower, just cutting showers by 1 minute can make a difference on energy and water consumption.
- Limit the number of baths you take.
- Only run the dishwasher when its full, avoid running when partially filled.
Investing in Changes to Save…
The above are just a few examples of steps you can make right now. This is not an exhaustive list and if you look around your home I’m sure you could find other ways to reduce your energy usage. Some other ways to tackle energy consumption require an initial outlay, but can be worth it in the long run. Both for energy savings and for the comfort within your home. Some steps you can take are to look at:
- Draught proofing.
- Top up insulation. Make sure if doing this that it’s done effectively. it’s one thing to top it up but it needs to also be fitted correctly, look for a professional who can advise on this.
- Look for areas that might not be insulated at all, Underfloor insulation is an area that’s often overlooked but could save you 20-30% on energy bills and make your home more comfortable, a large number of older homes have suspended timber floors that are uninsulated, you can learn more about this on our website : https://greenhorizonenergy.co.uk/underfloor-insulation/
- Insulate water tanks or heating pipes. Uninsulated pipes can lose a lot of heat before they even reach your radiators. If those pipes are running in a cold floor void a lot of that heat is wasted.
Don’t Forget…
There are lots of small steps you can take now to start saving instantly, some bigger steps that will take more thought and some investment but ultimately will give greater energy savings overtime. Whatever you do, remember every little counts and its money in your pocket at the end of the day.
- Published in Uncategorized
Grade II Listed Property – A Recent Renovation in Burscough
One of our latest projects was to insulate the walls and roof of a Grade II listed stone built property in Burscough. Once a station house, Burscough Bridge railway station was closed to the traveling public in 2005 and was in need of a major refurbishment.
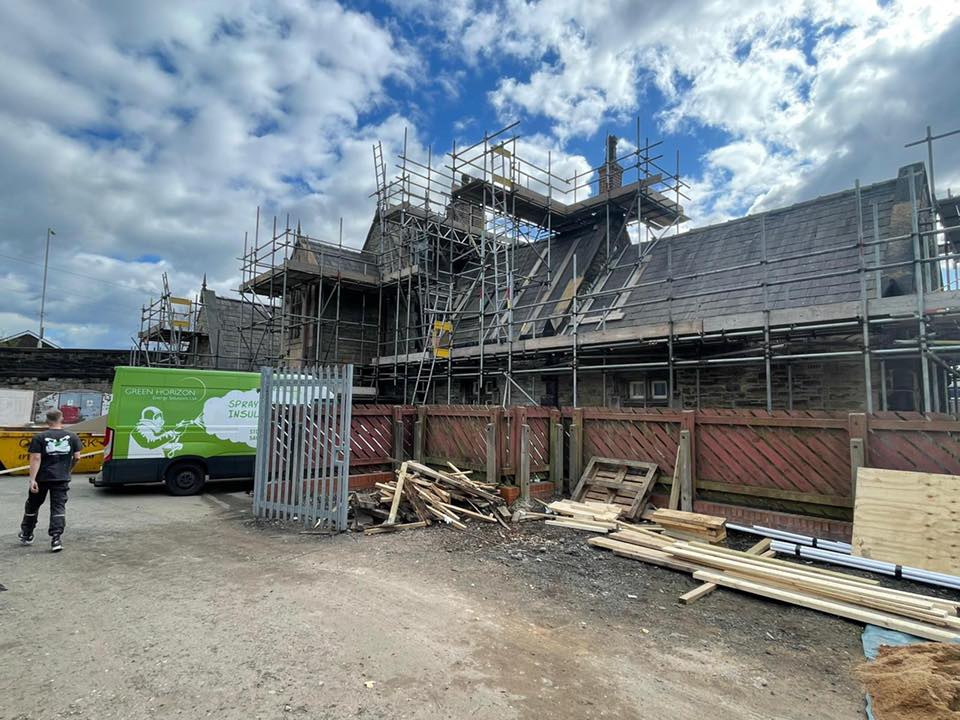
Local contractor JDC Construction & Developments ltd undertook the renovation works to bring this building back to life. Having worked with JDC previously on similar types of properties, they were confident that spray foam insulation was the perfect choice for their project, offering unrivalled air tightness, superior energy efficiency and speed of installation, they turned to us once again. We completed the works over a series of visits, fitting in with the contractors time frames and other works, in total we sprayed approx 285m2 of open cell insulation within a stud wall frame to the underside of the roof.
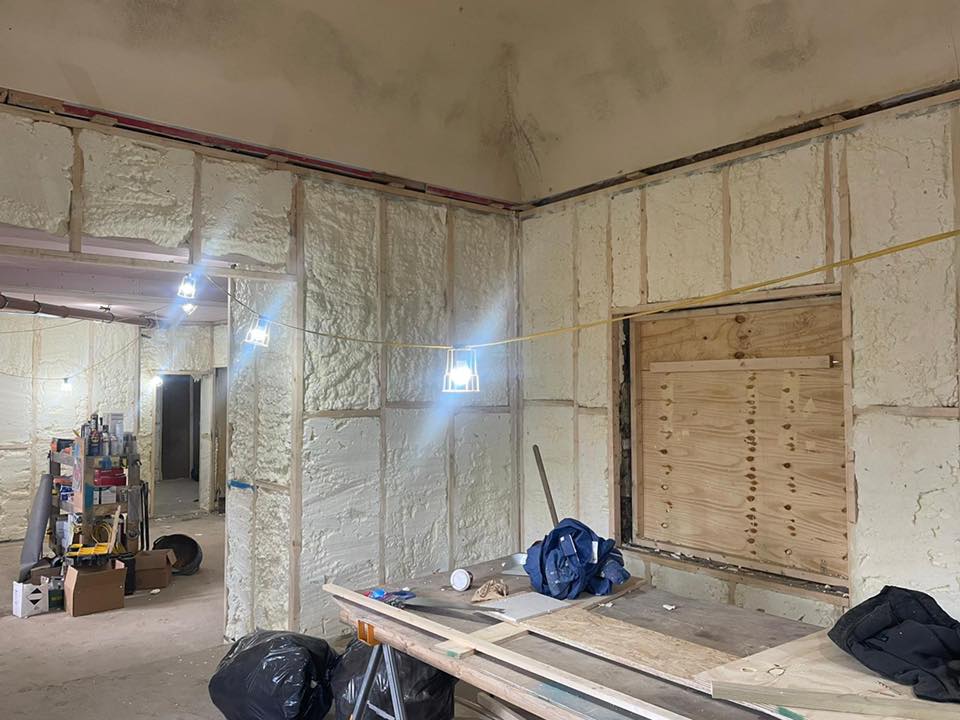
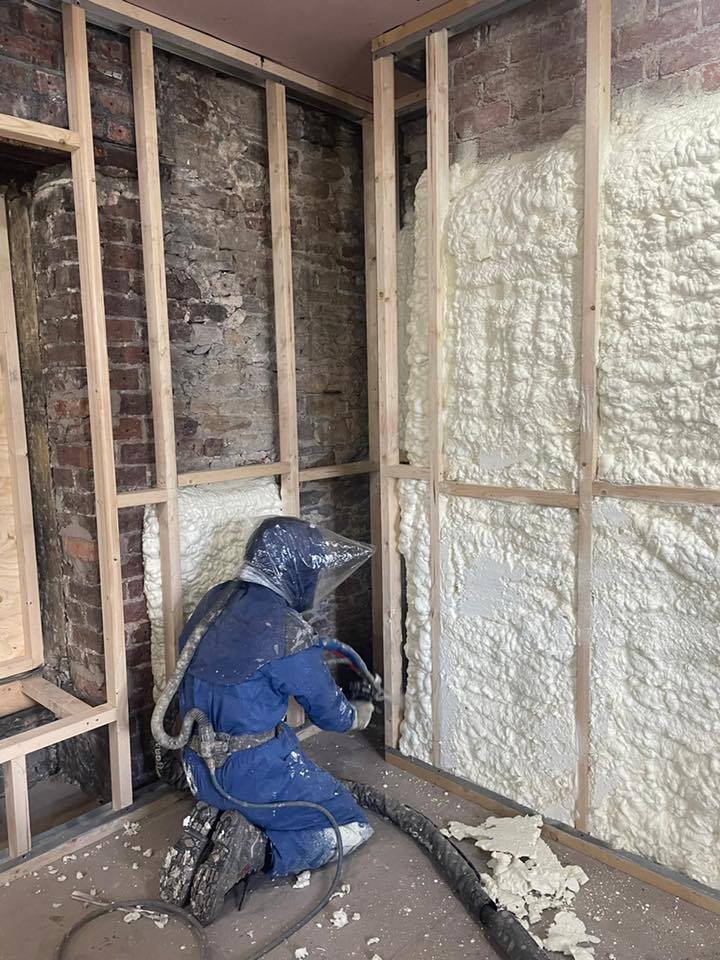
We sprayed Icynene open cell foam from Huntsman Building Solutions, BBA approved spray foam backed with a 25 year warranty.
- Published in Uncategorized
Spray Foam Contractor Training
To become a certified spray foam installer, all operatives must undergo a specific training program at the manufacturers training facility. Then, they are subject to on site audits for ongoing conformity.
All our operatives have attended extensive training sessions with Huntsman Building Solutions, the new home of Icynene. They have been trained on all aspects of spray foam insulation. From application of the different types of foam, health and safety, equipment maintenance and theory-based training. All to learn more about spray foam insulation products.
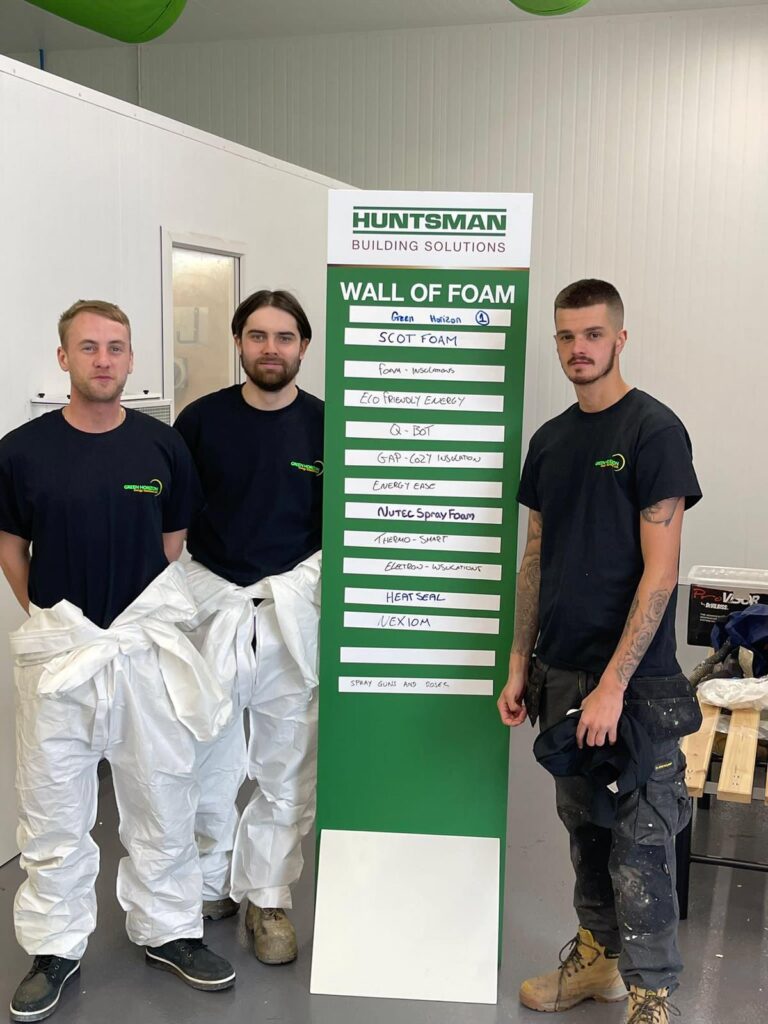
Specifying Spray Foam Insulation For New Builds & Extensions
Training is not limited to install staff alone. Our office staff have a wealth of knowledge too. Covering different types of spray foam, from their usages and different specifications to calculating U values.
It’s not enough to know how to spray foam insulation, we need to know so much more. Every house is different so we need to have a good understanding of suitability of each project. We have to consider how spray foam will interact with other building components. U value calculations and condensation risk analysis reports need to be produced for each project. New build properties and extensions will all have different target U values, and each property will have a different make up of materials. These differences will impact on U values and how they are calculated.
Building Projects
We can assist with your building project right from the start. We can calculate U values and provide all the required information for building control to pass off your insulation works before we commence the installation. All our insulation installs come with a 25-year warranty on completion.
Retro Fit Insulation
We can also specify insulation for a retro fit project, be it underfloor or roof insulation you require. Most retro fit projects won’t need to meet the same specification as a new build or extension. They will still need to be assessed for suitability. As with new builds not every house is the same. A balanced approach should be taken when assessing suitability of your home for retro fit insulation. We can gather information from you on the phone or by email in the first instance and move on to a full site survey later, should it be required.
- Published in Uncategorized
The Importance of Airtightness in a Building Envelope
What do we mean by airtightness?
Many people get confused and think that if somethings airtight it’s going to trap moisture and cause materials to sweat, especially where spray foam insulation is concerned.
Put simply, something that’s airtight has the ability to stop mass transfer of air. Which does not always mean stopping the ability to pass moisture vapour (breathe) if the product is breathable.
Air movement around poorly fitted insulation boards via convection will lose far more heat at a much faster rate than through heat loss via conduction of an airtight material.
If you were to leave your fridge door open just a small amount it would soon stop cooling things down. As little as a 5% gap around an insulation board can equate to a 50% loss in thermal efficiency.
Air leakage control is essential for improving
- Indoor air quality
- Limiting heat losses due to convection and mass transfer
- Avoiding mould growth
- Limiting airborne noise from the outside
- Improving effective U value
U Value
The U value of a building can be greatly reduced if the insulation product is not fitted correctly. We have seen countless times where an insulated boards are fitted in a vaulted ceiling and a hole is cut in the middle of the board for lighting. That hole goes directly through to a cold ventilated space above and will greatly reduce the U value of that section. This is due to the heat lost via convection through the hole. It will also allow cold air to push into the building from the outside.
Open cell spray foam insulation is an insulator and air barrier material all in one. It expands 100x to fill every gap and stops heat loss through air leakage, convection, and mass transfer. It’s a fully breathable product that will allow moisture vapour diffusion allowing materials in contact to continue to breathe.
Airtightness is key to a building’s energy efficiency; you can have all the insulation in the world but if you leave the front door open its always going to be cold. Control air leakage and you will be well on your way to achieving an energy efficient home.
Spray foam insulation is a key component in achieving an airtight building envelope.
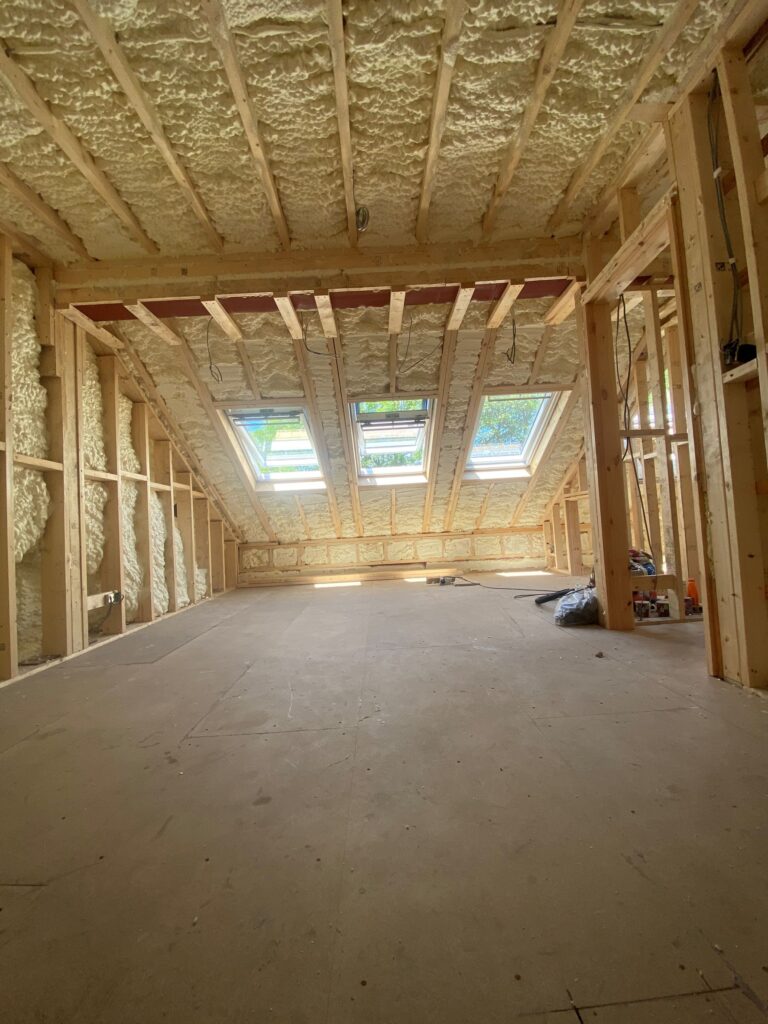
- Published in Uncategorized
Underfloor Insulation – The most overlooked insulation aspect of an older property…
Underfloor insulation in new builds and extensions is part of current building regulations and any new property must have the floor insulated. However, for many years this was completely overlooked. Many older properties were built with suspended timber floors and insulation was almost always overlooked. This means all that’s between you and the cold outdoor air are wooden floorboards, which is the main cause of cold floors. This, combined with expansion gaps on the building perimeter and holes for pipes and cables allows a considerable amount of cold air to push up into the building, making it even colder.
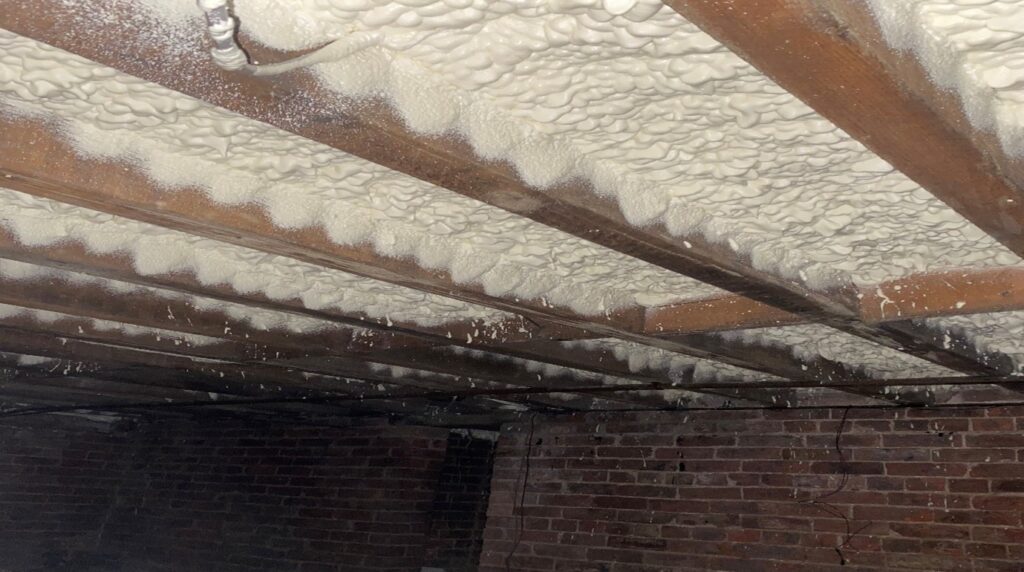
Uninsulated floors cause unwanted heat exchange between the warm air in the room and the cold floor. Heat exchange happens faster at higher temperature differentials. Basically a cold floor and warm room will always cool down much quicker once the heating is turned off.
Solution…
Insulating with open cell spray foam insulation is considered the most effective way to combat the problem of cold floors and unwanted draughts. Open cell spray foam is an insulator and air barrier combined. The breathability of the product means that it will allow moisture vapour diffusion. This stops materials from sweating and allows them to breathe. The air barrier status of the product stops cold air circulating through the material, acting in essence like a wind proof jacket.
The old way to insulate a suspended floor uses traditional loft insulation rolls. This is held in place with some sort of netting. The problem with this method lies in the fact that the material is not an air barrier meaning cold air can still circulate through the material and find its way through gaps in the floor. On the perimeter of all buildings is an expansion gap. Lying hidden below the skirting board, it is there to allow the floor to expand and contract with seasonal changes. It only needs to be a gap of a few mm but added up around the perimeter, it can equate to the size of a small window opening allowing cold air to continually push in. A tell tail sign of this gap can be seen on some properties with a very small dark line on carpets around the edge at the bottom of the skirting board where dust has blown up from the void below the floor.
One of the great benefits of open cell spray foam insulation is its ability to fill this gap. The product expands 100x its sprayed size and will fill every gap. Because it stays soft and flexible it will allow the floor to expand and contract also moving with the seasonal changes.

Need for Ventilation…
Ventilation of a suspended timber floor is an important aspect of keeping rot at bay. We have seen many examples of clients blocking their air bricks. Although this might offer some benefits in reducing draughts, it can cause problems with both wet & dry rot. When we insulate with spray foam insulation, we leave all air bricks clear from obstruction and material to allow for sub floor ventilation. Once the foam is installed it won’t matter about air bricks as the cold air will only circulate below the floor and won’t be given the chance to push up into any gaps above.
15% Heat Loss…
The Energy Saving Trust give a figure of 15% heat loss from a suspended timber floor. However, this figure does not consider draughts that push up into the property from the expansion gaps and other holes created from pipes and cables. It’s very hard to give an exact savings for any type of house. Obviously, every house is different. Some have small expansion gaps, some have large ones, some have bare floorboards or tiles, and others have big thick carpets. This will impact on the additional efficiency of the insulation. It’s not uncommon for our clients to report savings of over 20% on their heating bills after insulation. We also get constant feedback on the improved “comfort factor”. The temperature feels more stable and holding for longer even once the heating goes off.
We have done lots of work on Victorian properties that have exposed floorboards that have been sanded and varnished. These floors look great, but some have gaps of 3-4mm between every board and with gaps like that you might as well have the front door open. Floors like this will notice a huge difference to the heating costs and temperature within the house once insulated. The only downside we’ve had reported is a visual one. Once sprayed some floors will end up with some small white lines between the floorboards, this is where the spray has filled the gap. This is easily rectified with a furniture touch up pen and they also discolour over time. It’s a very small price to pay against what you will save on heating costs and for the comfort factor.
Growing Energy Costs…
With energy costs on a steep rise, there is no better time to insulate your suspended timber floor. Get in contact with us and we will be happy to provide you with a free no obligation quote. There are no pushy salesmen or ‘sign up now for X amount discount’, just a straightforward open honest approach. We will assess your property, take some measurements, and send you a quote by email that you can review in your own time.
- Published in Uncategorized
Getting To Know Spray Foam…
Have you ever wondered…
- What is spray foam?
- Is it safe?
- Does it give off gasses?
- Will it cause condensation?
- Will it cause rot?
- Will it trap moisture?
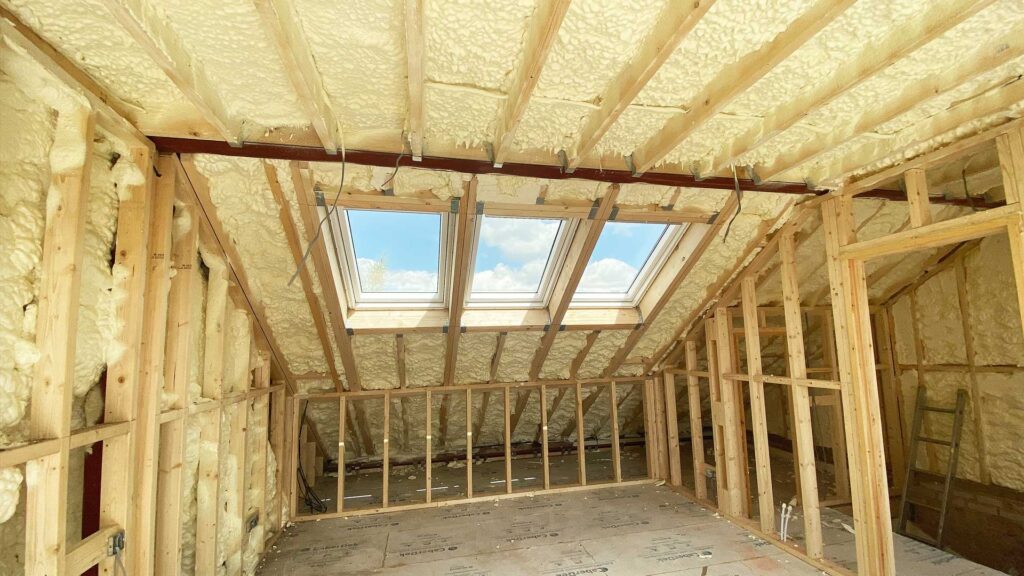
These are just some of the many questions & concerns potential clients raise with us, sometimes because of reading negative press or outdated misinformed information. Whatever your concern is and wherever its derived from, we’re looking to bust those myths and get to the facts about open cell spray foam.
In short open cell spray foam insulation is a polyurethane. It’s a plastic material that can be rigid or flexible – in open cells case, its flexible.
Why Icynene?
Green Horizon Energy Solutions work exclusively with Icynene from Huntsman Building Solutions, which is a water blown open cell foam. It uses water as a blowing medium and although there are some initial risks for the spray foam operative during the spraying process, once cured within a couple of minutes it is completely inert. Clients can return to the spray area within a couple of hours. The install of the product is a chemical process so we have to be mindful of this and for this reason the sprayers will wear a full air fed mask to prevent inhalation and to protect their eyes and face from encountering the raw material which has an exothermic reaction at 85c when expanding.
Icynene is water blown and therefore does not have an off-gassing period. Some other types of foam use chemicals in the blowing phase, trapping tiny bubbles of gas within the foam which take time to work their way out (off-gassing), whereas water blown foam creates C02 bubbles which pop as it expands and are replaced immediately with tiny air pockets. This means there is no off-gassing period and the only thing contained within the foam is air.
What is open cell?
Open cell foam means exactly what it says, the cells are open – this is important when preventing trapped moisture. It will allow moisture vapor diffusion also known as breathability. Breathability is a products ability to allow moisture vapor to diffuse through the material. Timbers need to breathe and by using an open cell foam this can still happen naturally. If you wrapped a bit of wood in a plastic bag it would eventually begin to sweat as the plastic bag is not breathable and there is nowhere for the moisture to go, but with open cell foam the moisture vapor can move through the material and into the atmosphere, working in essence, like a wind proof jacket as opposed to a plastic mac. We all know how you can sweat in a plastic mac as the moisture is unable to escape, yet in a windproof jacket this is not an issue because moisture is allowed to move freely through the material. By allowing materials to breathe you also in turn prevent the issue of rot.
Condensation concerns?
Once open cell foam is applied to the underside of a roof or floor boards, the risk of condensation is drastically reduced. Condensation forms when warm moisture laden air finds a cold surface and a dew point occurs which then cause the air to condensate on the cold surface, by spraying the underside of the roof you remove the cold surfaces for air to condensate on. There is 100x less moisture via diffusion than there is via convection, for example if you drilled a 2cm hole in a plasterboard it would carry 100x more moisture through than it would via diffusion alone.
The open cell nature of the foam will allow all materials in contact to continue to breathe naturally. Huntsman Building Solutions foams (Icynene), where developed in Canada in 1986 for timber framed houses that need to breathe. They have a long-standing reputation in the field of insulation with proven results in making homes more energy efficient and preventing any of the issues listed above. In the UK the foam has gone through numerous independent tests to determine the performance and deemed it suitable for the building market for both new and existing dwellings. It has achieved BBA & BDA approval and is approved for building warranties with NHBC as well as being recommended by the Energy Saving Trust.
Still want to know more?
We are always on hand to answer any further questions you might have regarding our open cell foam and we will always give you open and honest advise so get in touch to find out more.
- Published in Uncategorized
Government funding and grants, currently available for spray foam insulation
Of late we’ve been inundated with customers asking about government schemes, informing us of offers from companies offering grants of £1500 for spray foam insulation. We like to think we know our stuff when it comes to all things spray foam and we wanted to share our knowledge with you. Hopefully this article should shed some light on what is and isn’t available grant wise and help you avoid any potential hard sell tactics.
We appreciate that information can sometimes change quickly, therefore we always advise you to do your own research when looking at what funding is available. There are numerous reputable sources where you can check for the most recent funding options, The government website (www.gov.uk/topic/housing/funding-programmes) is always a good one to check, likewise the money saving expert website (www.moneysavingexpert.com) can be a great source of up to date information.
The most recent grant scheme available was the ‘Green Homes Grant Scheme’ this was a government funded scheme to help homeowners pay for the cost of energy efficiency measures to their homes by contributing 2/3rds of the cost to qualifying customers. When the scheme was launched in September 2020, the Government pledged £3billion to making UK homes greener, on the face of things the scheme looked great, but things unfortunately turned sour. Customers were struggling to find installers and there was a minefield of paperwork and regulations for installing companies making it almost impossible to get it set up effectively. The scheme was eventually cut short by the government and scrapped for new applicants in March 2021.
Although there may be some funding options for other measures within your home, spray foam insulation is not currently on that list. Currently there are several companies advertising grants of £1500 for spray foam insulation, saying all you need to do is fill in one form with your contact details and they will let you know if you’re eligible. At the time of writing this there currently are not any grants available for spray foam insulation for pitched roofs or underfloor. If you hear of any grants available, we advise you to do your own research. Find out where this funding is coming from and check its not just a sales ploy, and that you are not actually paying an inflated price for the services you require under the premiss you are qualifying for a grant.
- Published in Uncategorized
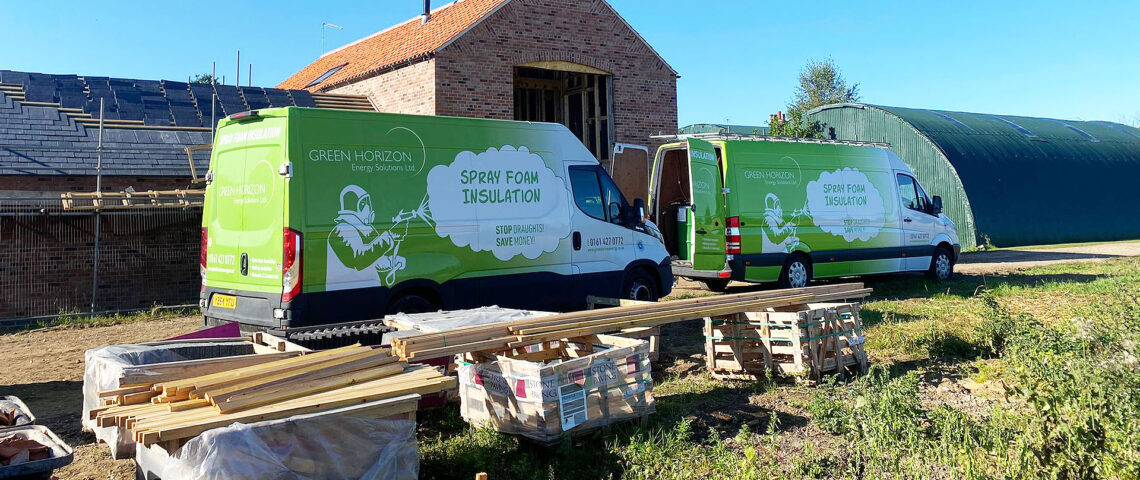
Breaking down the Myths – how to know what’s genuine when getting spray foam quotes.
- Published in Uncategorized